rtaylor
PRO Member
I need some advice on construction of, and, cutting segments for a feature ring. Although I have done this lamination before, I think I am making it more difficult than it needs to be so I thought I would ask how some of you do it. I use a Dubby sled for cutting segments and have found it to be extremely accurate. When it comes to feature rings that require each individual segment to be cut as a single segment rather than cutting from a strip things get a little more difficult. Before I get to that point in construction however what is the best way to cut a second generation with extreme accuracy in the following example....
I find that using my equipment is very difficult to hit the same position each time, especially when you are using the points of the lamination to run along a miter fence. In this next example image, the desired feature is achieved and now they need to be cut apart at correct angle cut for segmenting.
I have been cutting the repeating units apart with a band saw then cutting the angle on each individual segment. The ring is 2.25 inches tall so holding that piece and cutting it with a sled and the table saw gets pretty dicey...Anyone who has advice or methods please let me know. I could sure use some help.
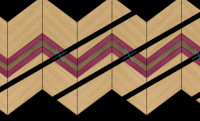
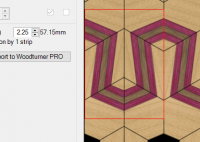