We had a similar discussion regarding gluing and aligning segments back in Dec 2022 on the segmented turners forum. Scott Gordon's post (below) described the problem, and a solution.
Scott's Post
I use a homemade jig whereby I glue on a single segment at a time. I like this approach over the stomper as it gives me more flexibility in terms of the number of segments and degrees in between segments, or even using different settings from row to row. I also use Woodturner Pro and/or Segment Pro for the layout information.
As I was assembling some bowls, I noticed especially as I was putting on the flat ring at the top that there was much less overlap than I was expecting. I then realized that the reason for this is the software reports the diameter of the open segment rings, but that is different than the radius where the segment has to be placed if using the jig I have (or even the Tom Lohman jig). The problem is that the outside segment corners stick out beyond the intended radius. Therefore, if placing the segment at the diameter/radius calculated by the software, the resulting radius will actually be less. The amount of error is going to be greater when the # segments per row is lower and the diameter is larger.
The attached photo shows what is happening. The red line reflects the calculated radius. However, on the horizontal line, there is the additional green segment to the left of the red line showing the part that is not included in the calculation. If you place the segment with the outside corner where the red line ends, you have actually reduced the overall diameter.
This is an easy correction using the lessons of geometry I learned from a few decades ago. (Okay - it was many decades, but the Pythagorean theorem still works!) To correct in Excel, the formula is: =SQRT(([Outside Diameter] / 2)^2 + ([Segment Edge Length] / 2) ^ 2)) This is the good old:
a^2 + b^2 = c^2
where a would be the Outside Diameter divided by 2 and b would be the Segment Edge Length divided by 2. c is then the corrected radius to place the segment which included the green segment of the horizontal line.
Attachments
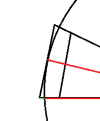
Radius correction.png